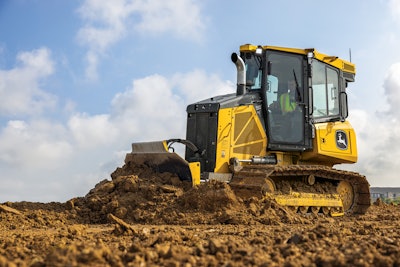
Machine control continues to propel dozer and excavator productivity and performance forward as contractors maximize these offerings to contribute to their bottom line and increase the return on investment.
New Machine Control Developments Demonstrate Improvements
The market offers new developments that have changed and improved over the past several years.
Over the past five years, advancements in GNSS receivers have significantly improved their reliability and performance, most notably for operators working in GNSS-compromised areas, noted Cameron Clark, Trimble business area director, earthmoving industry, civil construction field systems.
For example, Trimble’s MS9X6 receivers enable contractors to operate in areas previously unsuitable for GNSS-based solutions.
“These advancements can also remove the need for Universal Total Station or robotic total station setup, because contractors have access to these enhanced GNSS capabilities, allowing for greater flexibility and efficiency on the job,” Clark added.
Another development is the reliance on machine control solutions, which have become indispensable for many contractors, Clark said, adding any disruption in these systems — like a simple cable malfunction — can impact productivity as significantly as a machine experiencing a hydraulic issue.
New operator assistance features also have been introduced, allowing machine control to extend beyond basic implement control.
“Aiding with the skilled labor shortage, Trimble’s advancements in steering systems for dozers and compactors can maintain machine alignment automatically - no specialized skill required,” said Clark, adding Trimble has a white paper detailing features on compactors that reduce overlap, contributing to lower emissions and fuel use.
Advancements in steering systems for dozers can maintain machine alignment automatically without requiring specialized skills.Trimble
“Connectivity on the jobsite has also improved, enhancing communication between the jobsite to the office and back to the jobsite,” said Clark. “This connectivity allows for faster, more efficient updates on project details and design changes, while improved remote troubleshooting tools and software upgrades make it easier for contractors and their dealers, like SITECH, to support field operations directly.”
SmartDetect and Advanced Vision systems are John Deere’s newest offerings. “The Advanced Vision systems improve operator situational awareness, assuring that the eyes of the operator can see jobsite surroundings,” noted Matt Costello, John Deere product marketing manager.
“This system builds on the rear-view camera systems of the past by adding more cameras in the positions of rear-view mirrors and enlarge the sight lines. We have also incorporated upgradability to our newest vision system in SmartDetect,” he added.
SmartDetect is a camera system that provides real time alerts to the operator. It will highlight and detect all objects behind the machine. SmartDetect has a unique audible and visual alert when a bystander is detected. This system increases and enhances a wider field of view.
“When skilled labor can be hard to find, solutions like SmartDetect provide confidence and situational awareness to all operators,” said Costello.
SmartGrade, which John Deere developed in 2016 on the construction dozers, has grown to be on more than 20 models of John Deere equipment today. This year, the company launched the next generation of SmartGrade on dozers and large frame CTLs. “John Deere now owns the hardware, software and control,” says Costello. “We provide flexibility with the GNSS provider to allow contractors an easier path to put Deere on their jobsite.”
The next generation of SmartGrade offers SmartGrade Ready with 2D grade control in a new 10.1- or 12.8-inch touch screen display.
“An operator can easily toggle between 2D and 3D depending on where they are on the jobsite and which phase of the project,” Costello noted. “It includes the ability to plug and play laser as well proving that needed edge to move into any jobsite. The new touchscreen displays have tips on setting up the machine as well as the operator manuals right on the display.”
All the John Deere technology solutions are tied to Operations Center to provide reporting and data on usage, alerts, productivity, and other relevant information to manage the business.
The machine control hardware, like other technology hardware, has improved over time like smaller and faster processing sensors, noted Scott Hagemann, Caterpillar market professional.
“Caterpillar has software releases that include new features on an annual basis: Steer Assist, Blade Load Monitor on dozers, Steer Assist on excavators, E-fence on mastless motor graders.”
Enhanced Productivity, Performance
Speaking to how the technologies contribute to equipment productivity and performance, Costello pointed out grade control technology significantly enhances the capabilities of experienced operators while helping novice operators feel comfortable on the jobsite more quickly, allowing contractors to maximize their available labor.
“John Deere SmartGrade features remote display access to its monitor, enabling remote troubleshooting, training, and assistance with operator setups,” he said. “With the next generation of SmartGrade, these functions can be utilized for both 2D and 3D solutions.
“Additionally, John Deere SmartGrade includes wireless data transfer, allowing jobsite files to be sent to multiple machines remotely. This feature streamlines the process of updating designs, as any necessary changes can be communicated without the need to visit each machine, thus improving efficiency on the jobsite.”
With Steer Assist, a dozer will not only control the blade elevation, but it will also steer the machine to follow a 3D line – center of road, edge of curb, center of ditch, said Hagemann, adding that for blade load monitoring, the machine tells the operator the amount of load on the blade.
Machine control technology makes it possible for operators to cut to grade accurately on the first pass, eliminating the need for estimating between stakes or an operator’s interpretation, Clark noted.
“In automatic mode, the dozer system follows commands precisely,” he added. “This presents one example of how the shortage of expert operators is being addressed. Expert operators are hard — if not impossible — to find, but machine control can increase the productivity of less experienced operators and enable them to produce consistent results.
“The data coming from these operations also help to identify training opportunities to make all your operators your best operator.”
Clark noted to think of the process like a 3D printer.
“You start with a detailed 3D design, which then ‘prints’ the exact model you envisioned. Using Trimble Business Center, contractors can create a 3D model, send it to Trimble Earthworks, and then leverage semi-automatic controls to build the model efficiently and precisely,” he added.
Addressing how machine control technology for equipment such as dozers and excavators can derive savings in time and/or money, Clark noted that machine control technologies on dozers provide several time and cost savings, including:
- Minimizing rework by completing the task correctly on the first pass.
- Giving operators all the information they need in the cab, eliminating the need to wait on grade checkers or subcontractors. “In some cases, this can also free up staff to do other tasks instead of placing stakes or performing a grade check,” he added.
- Working more efficiently, which uses less fuel and translates to lower costs and lower carbon emissions while also reducing wear and tear on machines.
- Needing fewer machines. “For example, the need for a dozer to clean up after an excavator or a grader to finish after a dozer can be eliminated with machine control,” Clark said.
- Ensuring specs are being met so the right amounts of material are being used, and the right amounts are being hauled away so there is not the need to bring back any material at a high cost.
- Maximizing productivity and efficiency at every step of the process.
- Being able to get the job done right and in the fewest passes helps a contractor’s bottom line, noted Costello.
Contractors can create a 3D model, send it to Trimble Earthworks, and then leverage semi-automatic controls to build the model efficiently and precisely.Trimble
“With SmartGrade technology on a dozer, an operator can be more efficient with each pass and move the material the least amount of times,” he said. “This equates to lower hours on the machine per job, less fuel burnt, the ability to bid confidently, and the flexibility to use a machine from site development to finish grading. On a jobsite, the more efficient each machine can be in its task, the easier it is for the next one.”
Case in point: an excavator working on a cut.
“If they have any level of grade control such as laser, 2D, or even 3D SmartGrade, they can get their cuts closer to grade,” Costello said. “Once the excavator moves on and a dozer comes in, it can get to finish grade in fewer passes. This can equate in a more accurate account of other materials such as aggregate.
“The more accurate the subgrade, the lower chance of overlaying the expensive items like rock and concrete. This will reduce the need for any costly rework as a project progresses.”
Every contractor who uses machine control technologies will save time and money, said Hagemann, adding contractors using Caterpillar machine technology have gotten jobs done faster, which saves time and allows them to complete more projects per year.
“Therefore, they can make more money during the year and by grading at tighter tolerances, they save materials,” he adds.
Trimble’s MS9X6 receivers enable contractors to operate in areas previously unsuitable for GNSS-based solutions.Trimble
Greater ROI
Addressing how contractors can employ technology in effective ways as to maximize their return on investment, with the John Deere Operations Center, contractors can monitor the utilization of machine features, allowing them to track how much time SmartGrade is being used throughout the day based on the project’s current phase, including idle time and other technology solutions.
The next generation of SmartGrade allows contractors to begin with 2D grade control and plug-and-play laser capabilities, with the option to easily upgrade to full 3D capabilities through a finishing kit as their business grows or as they take on more engineered projects.
“Machine control technology is increasingly being adopted on jobsites, and priority number one is ensuring strong support,” said Costello. “John Deere’s dealer network is equipped with factory-trained precision construction specialists to maximize uptime, and a dedicated field team provides assistance with everything from training to troubleshooting.
“This support extends to the Dealer Technical Assistance Center where precision construction experts focus on jobsite readiness, continuous improvement, and training.”
Machine control technology requires a process change in the company, Hagemann pointed out.
“It is a new way of bidding, operating, and managing projects,” he added. “You have fewer survey costs for staking and you operate less so you save labor, fuel, and material costs.”
It is important for contractors to know they do not need to go all in when they are ready to adopt machine control technology, Clark noted.
“The first step should be talking with your dealer, such as SITECH for Trimble solutions, and making sure they understand your business and your goals, and the solutions available to you,” Clark said. “Your dealer and technology provider should also be your partner when it comes to providing the training and in-field/office support when needed.
“When you have these supports in place, there is no need to be afraid of machine control technology. It is worth the time and effort to learn what it makes possible with less resources, how it can improve workflow even when you do not have a 3D model, and how to leverage the automatics of machine control.”
Reduced Rework, Cost Overruns, Material Use
Hagemann noted that work is reduced because of always having the jobsite on the screen, in front of the operator showing cuts and fills, and because a contractor no longer has to wait on a surveyor to stake the jobs.
“Rework is less because you have a full-time grade checker in the cab on the display so you grade to the correct elevation the first time and since you can grade with tight tolerances, you save material,” he added.
Machine control adds confidence that the job is getting done right the first time, said Costello, adding it gives contractors the ability to manage their costs like labor, fuel, and supplies.
“Having a good understanding of this information not only helps on the job today, but allows much more competitive bidding down the road,” Costello said. “Unplanned rework can make or break a project and providing solutions like SmartGrade that are easy to use, flexible, and maintain productivity give contractors the tools they need to complete jobs.”